100L 7.5KW Stirring Ball Grinder Equipment for Small-Batch Experiments
The principle of the stirred ball mill is that the main shaft drives the stirrer to rotate at high speed, causing the grinding media in the stirring bucket to move irregularly. This disordered movement generates collisions, squeezing, friction and shearing of the grinding media, thereby crushing and fine grinding the materials. The whole machine mainly consists of the stirring bucket, stirring device, frame, electrical control and other auxiliary devices (such as: It is composed of a material pumping circulation device, a water-cooled jacket device, a heating temperature control device, etc.) It is particularly suitable for wet grinding of small-scale, medium-scale and large-scale materials, with high grinding efficiency and small particle size. Dry grinding is suitable for materials with certain characteristics, such as materials that need to have certain fluidity, not easy to form plates, settle at the bottom or stick to the wall, and can well meet various process parameter requirements.
A. Application of the stirring Ball Mill
The equipment is simple, occupies a small area, has the advantages of low energy consumption and low price, and is the preferred equipment for small-batch experiments in schools and research institutions. It is widely used in the production fields of various ultrafine powders such as zirconium silicate, zirconia, electronic materials, magnetic materials, coatings, graphite and pharmaceuticals.
B. Technical Parameters
Model |
MBM-100L |
Volume of the ball mill jar (ML) |
100L*1 |
The structure of the ball mill jar |
1. Structure of the ball mill tank: The cylinder is equipped with a water-cooled jacket, and the inner cylinder is of a straight structure. The inner cylinder is made of 304 stainless steel. 2. A ground opening is made on the bottom plate of the cylinder (which serves as both the discharge and volleyball opening, as well as the pump circulation material opening), and a stainless steel screen with a 2mm spacing is matched with the ground opening. 3. The cylinder cover is divided into two parts, made of stainless steel 304, and is equipped with a feeding port and an adjustable rubber stopper. |
Stirrer |
304 stainless steel stirring rod |
Stirring speed |
40-145r/min |
Feed particle size |
≤10mm |
Output particle size |
The minimum size can be as small as less than 1μm (the particle size of the output varies depending on the material and process) |
Loading capacity |
About 40 liters |
Speed regulation mode |
Variable frequency speed regulation |
Transmission mode |
Belt drive |
Discharge method |
The bottom of the bucket is equipped with a stainless steel screen with a spacing of 2mm, which is flush with the bottom of the cylinder. A stainless steel 304 material discharge valve with a diameter of DN15 is used and connected to the diaphragm pump pipeline for a circulating ball mill. The circulating pump directly draws out the material. |
Pneumatic diaphragm pump |
Model QFQ-25PTFE(stainless steel base + three diaphragms +PTFE diaphragms), flow rate 0-7m³/H, head 84 meters, circulation pipes and valves are made of stainless steel 304 material. |
Working voltage |
Three-phase 380V, 50HZ |
The power of the main motor and the frequency conversion power |
7.5KW (The motor brand is Dedong and the frequency converter brand is Delixi) |
Reducer |
Worm gear reducer WPX155-B 1:10 |
Explosion-proof box |
Explosion-proof grade BT4, explosion-proof pipe DN20, integrated with equipment installation |
Reference weight of the equipment (KG) |
Approximately 590 kilograms |
Reference dimensions of equipment shape (mm) |
Length 1200mm x width 900mm x height 1500mm |
C. Product Features
1. The equipment has a simple structure, low noise, is easy to move, and does not occupy space in the working environment.
2. Compared with the principles of other ball mills, due to the different running trajectory curves of the grinding media in the stirring barrel, it features a higher stirring speed, lower power consumption, and the highest ball milling efficiency.
3. The particle size of the material can be controlled by optimizing the proportion of different balls, speed, ball milling time and other related processes to regulate the curve distribution of the fineness of the material. The operation is very flexible and practical.
4. According to the characteristics of the materials, a customized heating temperature control device can be selected to control the heating range of the materials, a water-cooled jacket device to control the cooling of the materials, and a material pumping circulation device to control the fineness of the ball-milled materials.
5. Through electrical control, the total timing, interval downtime or continuous, speed-regulating cycle can be achieved to meet various process requirements of materials.
6. The equipment can be customized. During the ball milling process of the materials in the mixing tank, inert gas protection is carried out to prevent the materials from being oxidized. Even for flammable and explosive materials, the equipment can be customized according to explosion-proof requirements.
7. According to the material characteristics, the inner wall of the mixing tank is lined with non-metallic materials (such as corundum ceramic, zirconia, nylon, polytetrafluoroethylene, polyurethane, etc.), and the outer layer of the stirring rod is made of different materials to reduce the probability of material contamination and improve the purity of the material.
D. Pictures related to the stirred ball mill products
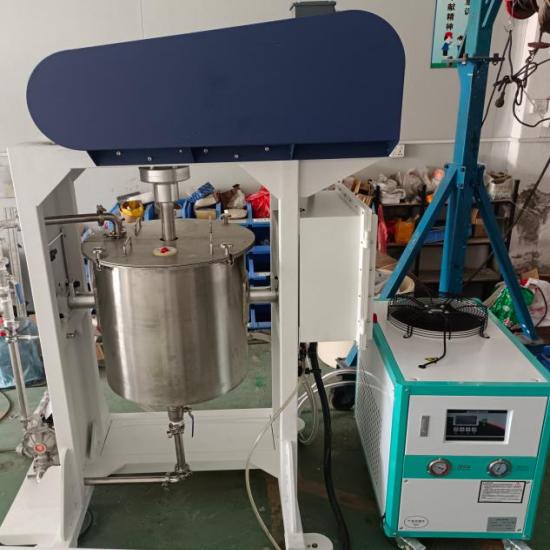